Proces produkcji papieru stanowi fascynującą podróż od surowca do gotowego produktu, którym posługujemy się codziennie. Współczesne zakłady papiernicze wykorzystują zaawansowane technologie, aby przekształcić drewno, makulaturę czy inne materiały celulozowe w wysokiej jakości papier. Zrozumienie tego procesu pozwala docenić złożoność wytwarzania materiału, który wydaje się tak powszechny i oczywisty.
Każdy etap produkcji papieru wymaga precyzyjnego kontrolowania parametrów technologicznych, od przygotowania surowca po ostateczne wykończenie produktu. Nowoczesne metody produkcyjne łączą tradycyjne techniki z innowacyjnymi rozwiązaniami, zapewniając efektywność oraz wysoką jakość finalnego wyrobu.
Przygotowanie surowców do produkcji papieru
Surowce do produkcji papieru obejmują przede wszystkim drewno iglaste i liściaste, makulaturę oraz alternatywne materiały jak słomę czy bambus. Drewno iglaste dostarcza długich włókien celulozowych, które nadają papierowi wytrzymałość, podczas gdy drewno liściaste zapewnia krótkie włókna odpowiedzialne za gładkość powierzchni.
Proces rozpoczyna się od przygotowania drewna, które musi być pozbawione kory i pocięte na odpowiednie fragmenty. Kłody trafiają do specjalnych maszyn zdzierających korę, a następnie do rębaczek, gdzie zostają pocięte na jednolite zrębki o długości 15-25 milimetrów. Rozmiar zrębków ma kluczowe znaczenie dla efektywności kolejnych etapów produkcji.
Makulatura jako surowiec wymaga dokładnego sortowania i oczyszczenia z zanieczyszczeń. Proces ten obejmuje usuwanie elementów metalowych, plastikowych oraz innych niepożądanych materiałów. Jakość makulatury bezpośrednio wpływa na właściwości końcowego produktu i efektywność całego procesu produkcyjnego.
Proces roztwarzania i oczyszczania masy papierniczej
Roztwarzanie masy celulozowej stanowi kluczowy etap, podczas którego surowce zostają przekształcone w masę nadającą się do formowania papieru. W przypadku drewna proces ten odbywa się w wielkich kotłach warzelnych, gdzie zrębki poddawane są działaniu wysokiej temperatury i chemikaliów alkalicznych.
Temperatura warzenia osiąga 160-170 stopni Celsjusza, a proces trwa od 1,5 do 3 godzin w zależności od rodzaju surowca. Chemikalia używane w procesie warzenia to głównie wodorotlenek sodu i siarczek sodu, które rozpuszczają ligninę łączącą włókna celulozowe w drewnie.
Po zakończeniu warzenia masa trafia do systemu oczyszczania, gdzie usuwane są pozostałości ligniny oraz inne zanieczyszczenia. Oczyszczanie masy papierniczej odbywa się w kilku etapach z użyciem sit, cyklonów oraz flotacji, które separują niechciane cząstki na podstawie różnic w gęstości i rozmiarze.
Masa z makulatury wymaga innego podejścia – roztwarzanie makulatury odbywa się w pulperach z użyciem wody i środków chemicznych neutralizujących farby drukarskie. Proces odbarwiania usuwa atramenty za pomocą flotacji lub przemywania, przywracając masie odpowiednią białość.
Wybielanie i przygotowanie masy do formowania
Proces wybielania masy celulozowej ma na celu uzyskanie odpowiedniej białości oraz usunięcie pozostałości ligniny. Współczesne metody wykorzystują sekwencje ECF (Elemental Chlorine Free) lub TCF (Totally Chlorine Free), które są bardziej przyjazne środowisku niż tradycyjne wybielanie chlorem.
Wybielanie ECF wykorzystuje dwutlenek chloru, nadtlenki oraz ozon w kontrolowanych warunkach temperaturowych i pH. Każdy etap wybielania wymaga precyzyjnego dozowania chemikaliów oraz monitorowania parametrów, aby uzyskać jednolitą białość bez uszkodzenia włókien celulozowych.
Po wybieleniu masa zostaje rozcieńczona do odpowiedniego stężenia, zwykle 0,5-1% suchej masy. Przygotowanie masy do formowania obejmuje także dodawanie środków pomocniczych: klejów zwiększających wytrzymałość na mokro, środków wypełniających poprawiających nieprzezroczystość oraz barwników nadających odpowiednią barwę.
Masa musi być dokładnie wymieszana w specjalnych mieszadłach, aby zapewnić równomierne rozprowadzenie wszystkich składników. Kontrola jakości masy papierniczej na tym etapie obejmuje badanie konsystencji, pH, temperatury oraz stopnia zmielenia włókien.
Formowanie arkusza papieru na maszynie papierniczej
Maszyna papiernicza stanowi serce całego procesu produkcyjnego, przekształcając płynną masę celulozową w ciągły arkusz papieru. Proces rozpoczyna się w skrzyni natryskowej, gdzie masa zostaje równomiernie rozprowadzona na ruchomej siatce formującej.
Sekcja formowania składa się z siatki, na której następuje odwadnianie masy pod wpływem grawitacji oraz podciśnienia. Woda przesącza się przez siatkę, pozostawiając włókna celulozowe, które splatają się tworząc strukturę papieru. Prędkość siatki oraz intensywność odwadniania wpływają na gramaturę i strukturę powstającego arkusza.
Świeżo uformowany arkusz o wilgotności około 80% przechodzi do sekcji prasowania, gdzie zostaje umieszczony między filcami i poddany działaniu wałków prasujących. Prasowanie papieru usuwa dodatkową wilgoć oraz wygładza powierzchnię, zwiększając jednocześnie gęstość i wytrzymałość materiału.
Na tym etapie arkusz osiąga wilgotność około 45-50% i zyskuje wystarczającą wytrzymałość, aby przejść do kolejnej fazy produkcji. Kontrola grubości arkusza odbywa się automatycznie za pomocą systemu skanującego, który reguluje natrysk masy w przypadku wykrycia nierówności.
Suszenie i wykańczanie papieru
Proces suszenia papieru odbywa się w długiej sekcji składającej się z ogrzewanych cylindrów, przez które przeprowadzany jest arkusz. Temperatura cylindrów waha się od 150 do 200 stopni Celsjusza, a proces jest kontrolowany tak, aby uniknąć nadmiernego naprężenia lub uszkodzenia struktury włókien.
Arkusz przechodzi przez kolejne grupy cylindrów suszących, stopniowo tracąc wilgoć do poziomu 6-8%. Suszenie wieloetapowe zapewnia równomierne usuwanie wody oraz zapobiega odkształceniom, które mogłyby powstać przy zbyt gwałtownym odwadnianiu.
Kalendrowanie papieru następuje po wysuszeniu i polega na przepuszczeniu arkusza przez system wałków metalowych pod wysokim ciśnieniem. Proces ten wygładza powierzchnię, zwiększa gęstość oraz poprawia połysk papieru. Intensywność kalendrowania zależy od przeznaczenia produktu finalnego.
Końcowe wykończenie może obejmować powlekanie powierzchni papieru specjalnymi preparatami poprawiającymi właściwości drukowe lub nadającymi szczególne cechy jak wodoodporność. Powłoki są nanoszone za pomocą aplikatorów w kontrolowanych warunkach temperatury i wilgotności.
Kontrola jakości i pakowanie gotowego produktu
Kontrola jakości papieru przeprowadzana jest na każdym etapie produkcji, ale szczególnie intensywnie przed pakowaniem gotowego produktu. Badania obejmują gramaturę, grubość, wytrzymałość na rozciąganie, odporność na przebicie oraz właściwości powierzchniowe.
Automatyczne systemy monitorowania mierzą parametry w czasie rzeczywistym, pozwalając na natychmiastową korektę procesu w przypadku wykrycia odchyleń od normy. Laboratoryjne badania papieru weryfikują właściwości chemiczne, pH, zawartość popiołu oraz stabilność wymiarową.
Gotowy papier zostaje nawinięty na tambory o średnicy kilku metrów, tworząc rolki główne o masie często przekraczającej kilka ton. Te ogromne rolki są następnie przecinane na mniejsze formaty zgodnie z zamówieniami klientów.
Pakowanie papieru wymaga szczególnej ostrożności, aby chronić produkt przed wilgocią i uszkodzeniami mechanicznymi. Rolki są owijane folią ochronną, a arkusze pakowane w wodoszczelne opakowania z odpowiednimi oznaczeniami dotyczącymi składowania i transportu.
Każda partia otrzymuje certyfikat jakości zawierający pełną specyfikację parametrów technicznych, co umożliwia klientom optymalne wykorzystanie produktu w ich procesach produkcyjnych. System identyfikacji produktu pozwala na pełną identyfikowalność i kontrolę jakości na każdym etapie łańcucha dostaw.
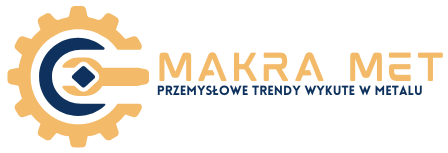
Makra-Met to profesjonalny portal branżowy, który od 2024 roku dostarcza ekspercką wiedzę z zakresu przemysłu metalowego. Realizując nasze motto „Przemysłowe trendy wykute w metalu”, łączymy praktyczne doświadczenie z innowacyjnym podejściem do branży.