Hartowanie to jedna z najważniejszych technologii metalurgicznych, która od wieków pozwala nadawać metalom wyjątkowe właściwości wytrzymałościowe. Ten skomplikowany proces termiczny wymaga precyzyjnego kontrolowania temperatury i czasu, aby osiągnąć pożądane charakterystyki materiału. Zrozumienie istoty hartowania metali okazuje się kluczowe dla każdego, kto zajmuje się obróbką cieplną lub projektowaniem elementów narażonych na wysokie obciążenia mechaniczne.
Definicja i podstawowe zasady hartowania
Hartowanie definiuje się jako kontrolowany proces obróbki cieplnej, polegający na nagrzewaniu metalu do odpowiednio wysokiej temperatury, a następnie gwałtownym jego schłodzeniu. Ta radykalna zmiana temperatury powoduje przekształcenia strukturalne w materiale, które znacząco wpływają na jego właściwości mechaniczne.
Podstawą procesu jest przekształcenie struktury krystalicznej metalu. Podczas nagrzewania atomy uzyskują większą mobilność, co umożliwia reorganizację sieci krystalicznej. Szybkie chłodzenie „zamraża” tę nową strukturę, uniemożliwiając atomom powrót do pierwotnego układu. W rezultacie powstaje struktura charakteryzująca się zwiększoną twardością i wytrzymałością.
Temperatura hartowania zależy od rodzaju stopu i pożądanych właściwości końcowych. Zbyt niska temperatura nie spowoduje wystarczających przemian strukturalnych, podczas gdy przekroczenie optymalnego zakresu może prowadzić do nadmiernego wzrostu ziarna i pogorszenia właściwości mechanicznych.
Rodzaje hartowania i ich zastosowanie
Hartowanie bezpośrednie polega na chłodzeniu materiału natychmiast po osiągnięciu temperatury austenityzacji. Ta metoda zapewnia maksymalną twardość, ale może powodować wysokie naprężenia wewnętrzne i zwiększoną kruchość materiału.
Hartowanie przerywane charakteryzuje się dwuetapowym procesem chłodzenia. Pierwszy etap obejmuje szybkie chłodzenie do temperatury powyżej punktu martenzytu, a następnie materiał jest przetrzymywany w tej temperaturze przed dalszym chłodzeniem. Ta metoda redukuje naprężenia wewnętrzne przy zachowaniu wysokiej twardości.
Hartowanie stopniowe wykorzystuje chłodzenie w kąpieli solnej lub metalowej o temperaturze zbliżonej do punktu przemiany martenzytycznej. Materiał jest przetrzymywany w tej temperaturze aż do wyrównania temperatury w całym przekroju, a następnie chłodzony na powietrzu.
Hartowanie powierzchniowe ogranicza proces tylko do zewnętrznej warstwy elementu, pozostawiając rdzeń w stanie plastycznym. Ta technika łączy wysoką twardość powierzchni z zachowaniem ciągliwości rdzenia, co jest szczególnie cenne w aplikacjach wymagających odporności na zużycie przy jednoczesnej odporności na pękanie.
Czynniki wpływające na skuteczność hartowania
Skład chemiczny stopu odgrywa fundamentalną rolę w określaniu hartowności materiału. Pierwiastki stopowe, takie jak chrom, nikiel, molibden czy wanad, zwiększają głębokość hartowania i stabilizują powstałe struktury. Zawartość węgla bezpośrednio wpływa na maksymalną twardość możliwą do osiągnięcia.
Szybkość chłodzenia musi być odpowiednio dobrana do grubości materiału i jego składu. Zbyt wolne chłodzenie nie zapewni pełnego przehartowania, podczas gdy nadmierna szybkość może spowodować pękanie lub nadmierną kruchość. Wybór ośrodka chłodzącego – woda, olej, powietrze lub specjalne polimery – determinuje intensywność odprowadzania ciepła.
Jednorodność nagrzewania wpływa na równomierność właściwości w całym przekroju elementu. Nierównomierne rozprowadzenie temperatury prowadzi do lokalnych różnic w strukturze i właściwościach mechanicznych, co może stanowić punkty koncentracji naprężeń.
Czas wygrzewania w temperaturze hartowania musi zapewnić pełną homogenizację struktury. Zbyt krótki czas nie pozwoli na kompletne rozpuszczenie węglików i wyrównanie składu chemicznego, podczas gdy przedłużenie procesu może prowadzić do rozrostu ziarna.
Mikrostruktura materiałów hartowanych
Martenzyt stanowi główną składową strukturalną materiałów hartowanych. Ta przesycona roztworu stały węgla w żelazie charakteryzuje się iglastą morfologią i wysoką twardością. Struktura martenzytyczna powstaje w wyniku bezdyfuzyjnej przemiany, która zachowuje przesycenie węglem z wysokotemperaturowego austenitu.
Austenit szczątkowy może pozostawać w strukturze hartowanej, szczególnie w stalach wysokowęglowych lub silnie stopowych. Ta faza metastabilna wpływa na właściwości mechaniczne i może ulegać przemianom podczas eksploatacji lub dodatkowej obróbki cieplnej.
Rozmiar i orientacja igieł martenzytu zależą od szybkości chłodzenia i składu chemicznego. Drobniejsza struktura martenzytyczna zapewnia lepsze właściwości mechaniczne dzięki zwiększeniu liczby granic między igłami, które działają jako bariery dla ruchu dyslokacji.
Naprężenia wewnętrzne nieodłącznie towarzyszą procesowi hartowania ze względu na objętościowe zmiany podczas przemian fazowych. Te naprężenia mogą być zarówno korzystne, tworząc naprężenia ściskające w warstwie powierzchniowej, jak i szkodliwe, prowadząc do pękania lub deformacji.
Właściwości mechaniczne po hartowaniu
Twardość hartowanego materiału wzrasta proporcjonalnie do zawartości węgla do poziomu około 0,6%, powyżej którego przyrost staje się mniej znaczący. Maksymalna twardość zależy głównie od zawartości węgla, podczas gdy pierwiastki stopowe wpływają przede wszystkim na hartowność i stabilność struktury.
Wytrzymałość na rozciąganie znacząco wzrasta po hartowaniu, często osiągając wartości powyżej 2000 MPa w stalach wysokowęglowych. Jednocześnie następuje drastyczne obniżenie plastyczności i ciągliwości, co czyni materiał bardziej podatnym na kruche pękanie.
Odporność na zużycie ścierne zwiększa się wraz z twardością powierzchni. Hartowana warstwa powierzchniowa charakteryzuje się wysoką odpornością na zadrapania i wciskanie, co jest szczególnie ważne w aplikacjach tribologicznych.
Granica zmęczenia może ulegać poprawie dzięki naprężeniom ściskającym w warstwie powierzchniowej, które przeciwdziałają propagacji pęknięć zmęczeniowych. Efekt ten jest szczególnie wyraźny w przypadku hartowania powierzchniowego.
Problemy i ograniczenia procesu hartowania
Pękanie hartownicze stanowi poważne zagrożenie, szczególnie w elementach o skomplikowanej geometrii lub dużych przekrojach. Przyczyny obejmują nadmierne naprężenia termiczne, zbyt szybkie chłodzenie lub obecność koncentratorów naprężeń.
Deformacje hartownicze wynikają z nierównomiernego chłodzenia i towarzyszących mu przemian objętościowych. Problem ten jest szczególnie istotny w przypadku elementów precyzyjnych, gdzie nawet niewielkie zmiany wymiarów mogą być niedopuszczalne.
Kruchość materiału hartowanego ogranicza jego zastosowanie w aplikacjach wymagających wysokiej odporności na uderzenia. Struktura martenzytyczna, mimo wysokiej twardości, charakteryzuje się niską energią łamania.
Kontrola głębokości hartowania może sprawiać trudności, szczególnie w przypadku elementów o zmiennym przekroju. Nierównomierna głębokość przehartowania prowadzi do lokalnych różnic we właściwościach mechanicznych.
Koszt procesu hartowania obejmuje nie tylko energię potrzebną do nagrzewania, ale także konieczność stosowania specjalistycznego sprzętu, atmosfer ochronnych i często dodatkowych operacji wykańczających, takich jak odpuszczanie czy szlifowanie.
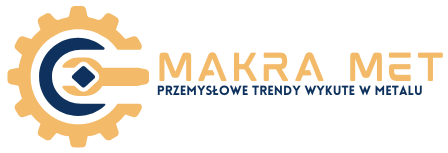
Makra-Met to profesjonalny portal branżowy, który od 2024 roku dostarcza ekspercką wiedzę z zakresu przemysłu metalowego. Realizując nasze motto „Przemysłowe trendy wykute w metalu”, łączymy praktyczne doświadczenie z innowacyjnym podejściem do branży.